El motor de émbolo vive hoy en día con la gran mayoría de la aviación general y la
aviación ligera y sirvió a todas las aeronaves autopropulsadas hasta la aparición del
motor a reacción.
El motor de émbolo, alternativo o de pistón, es un motor térmico, es decir
transforma la energía calorífica (combustibles) en energía mecánica (movimiento de la
hélice).
El motor esta compuesto principalmente por los cilindros que son cámaras herméticas de
forma cilíndrica en cuyo interior se desplaza un émbolo en movimiento ascendente y
descendente. El cilindro consta de cuerpo y culata. El cuerpo es la parte cilíndrica
propiamente dicha y la culata es la parte superior que hermetiza la cavidad junto con el
pistón o émbolo. La culata dispone de varios alojamientos para acoger a las bujías y a
las válvulas de admisión y escape. Ambos, cuerpo y culata, llevan practicadas a su
alredor muchas aletas para facilitar la refrigeación. (ver fig 1).
Los motores en función de la disposición de los cilindros pueden ser:
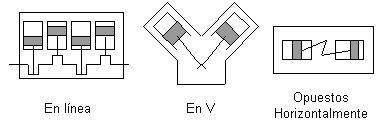
* En linea: Se disponen a modo de fila uno tras otro
consecutivamente. Con más de 4 cilindros ya se se presentan problemas para la
refrigeración de los cilindros interiores.
* Horizontales y opuestos: La gran mayoría de los motores de
baja potencia en aviación general. Se disponen normalmente 4 o 6 cilindros opuestos en el
plano horizontal. Esta disposición tiene muchas ventajas como reducción de las
vibraciones, del perfil...etc.
* Radiales: Tambien conocidos como motores de estrella. Los
cilindros se situan alrededor del cigüeñal en forma radial. Estos motores pueden tener
varias estrellas una detras de otra.
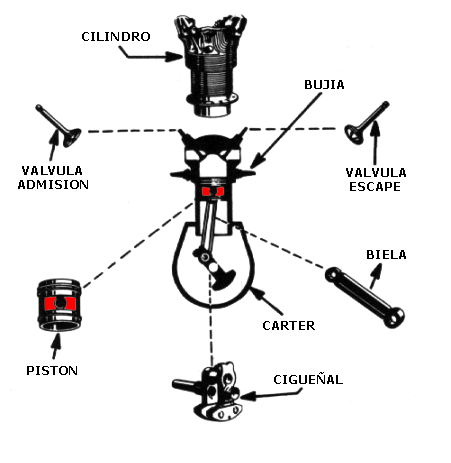
En función de la refrigeración los motores pueden estar refrigerados por aire o por
líquido. La refrigeración por líquido hoy en día esta obsoleta.
El funcionamiento se basa en comprimir una mezcla de aire y gasolina en los cilindros e
inflamar dicha mezcla con una chispa procedente de una bujía. La combustión de esta
mezcla provoca un gran incremento de la presión en el interior de dicho cilindro. Esta
presión la recibe el émbolo en un movimiento descendente.
La mezcla se obtiene del carburador o de un sistema de inyección.
Mediante un sistema biela-cigüenal el continuo movimiento escendente-descendente de los
émbolos es transformado en movimiento circular. Las bielas se unen a los émbolos en uno
de sus extremos y al cigüenal en otro, esta unión es por medio de cojinetes. La biela en
un complejo movimiento articulado transmite el movimiento alternativo al cigúeñal, el
cual ha modo de manivela lo transforma finalmente en rotación.
El cigüeñal es el eje principal del motor al cual se le acopla la hélice.
Los cilindros y el conjunto biela-cigüenal van montados en el cárter. El cárter es el
cuerpo estructural del motor y está sometido a grandes esfuerzos de torsión, vibración
e incluso el empuje de la hélice
Ciclo
del motor de cuatro tiempos
Antes definiremos algunos términos:
PMI: Instante en el cual el émbolo termina su carrera
descendente y comienza la ascendente, en este momento hay máximo volúmen en el cilindro.
PMS: Instante en el cual el émbolo termina su carrera
ascendente y comienza la descendente, en este momento el volúmen que existe entre la
parte superior del émbolo y la bóveda de la culata se denomina "cámara de
combustión".
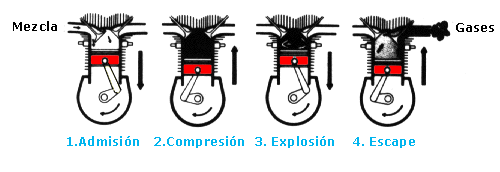
1. Admisión: La válvula de admisión se abre y émbolo partiendo del PMS se
desplaza hasta el PMI arrastrando por succión la mezcla.
2. Comprensión: La válvula de admisión se cierra y el embolo comienza su
carrera ascendente hacia el PMS comprimiendo la mezcla, ocupando esta mucho menos que
cuando entro en el cilindro.
3. Explosión: La mezcla es inflamada por la bujía y se produce un súbito
incremento de la presión que empuja el émbolo hacia abajo. La presión disminuye a la
vez que el émbolo se desplaza hacia el PMI. Es el único tiempo motor.
4. Escape: La válvula de escape se abre y el émbolo toma de nuevo carrera ascendente
hacia el PMS expulsando los gases quemados por el sistema de escape. En este momento el
cilindro está listo para realizar otro ciclo.
Distribución
Es el sistema encargado de accionar las válvulas
de admisión y escape en su debido instante. Las válvulas regulan la entrada y salida de
gases en los cilindros. La válvula de admisión controla la entrada de mezcla
aire-combustible en el cilindro y la de escape la salida de los gases quemados.
El mecanismo que desplaza las válvulas en un motor de cilindros horizantales y opuestos
es el árbol de levas, el cual es un eje normalmente de acero al cual se le practican unas
levas.
Las válvulas reciben el movimiento de las levas mediante el conjunto
taqué-empujador-balancín. Los taqués son varillas de gran resistencia las cuales tienen
un rodillo en uno de sus extremos . Este rodillo sigue fielmente el giro del eje y cuando
éste llega a la protuberancia de una leva transmite el movimiento empunjando el taqué
hacia arriba. El empujador transmite el movimiento del taqué al balancín, este
finalmente empuja la válvula hacia dentro abriendo el paso de gases. Cuando ninguna leva
acciona el rodillo las válvulas permanecen cerradas por la acción de un resorte.
Lubricación
del motor de émbolo
Las función principal de la lubricación es
disminuir el rozamiento de las partes metálicas en movimiento relativo mediante la
interposición de películas de aceite entre las piezas. Otras funciones secundarias son
la refigreración debida al baño de aceite de la piezas calientes del motor y evitar la
corrosión de los componentes del motor.
El sistema de lubricación estándar hoy en día es el de cárter húmedo, este sistema se
caracteriza por llevar el aceite en el propio motor, en el cárter.
Las partes fundamentales del sistema de lubricación son la bomba mecánica, el radiador y
el filtro.
La bomba mecánica normalmente es de engranajes, y su cometido es impulsar el lubricante a
través de todo el circuito de refrigeración. Las bombas de engranajes son normalmente de
desplazamiento constante y por tanto la impulsión del aceite depende de la rotación de
la bomba y directamente de la RPM del motor. Este tipo de bomba requiere un sistema de
regulación de presión mediante válvulas reguladoras.
El aceite en su función secundaria de refrigerante absorbe gran parte del calor generado
en la combustión y de esta manera se precisa un sistema de refrigeración de aceite.
El calor del aceite se disipa mediante un radiador que es un intercambiador de calor
expuesto a la corriente de aire, el cual enfría el aceite que circula por pequeños
conductos llamados celdillas. El radiador también va dotado de una serie de válvulas que
evitan sobrepresiones derivando el flujo fuera del radiador.
Finalmente el filtro tiene la función de retener los productos contaminantes como
partículas y lodos de la posible degeneración del aceite.
Instrumentos
indicadores
El buen funcionamiento del sistema de
refrigeración se puede verificar en función de la medición de dos variables: la
presión y la temperatura del aceite.
La presión de aceite se mide a la salida de la bomba mecánica normalmente y se indica en
la cabina del piloto mediante un manómetro.
Al igual que la presión, la temperatura se mide a la salida de la bomba y se indica
mediante un termómetro
El correcto estado de estas dos variables es vital para el correcto funcionamiento del
motor.
Bajas presiones de aceite se pueden deber a un nivel bajo de aceite, alta temperatura de
aceite o la válvula de alivio mal cerrada por suciedad. Altas temperaturas de aceite se
deben también a un bajo nivel de aceite, refrigeración ineficiente, filtros
sucios...etc.
Refrigeración
Los motores de combustión interna
generan una gran cantidad de calor. Se necesita entonces un sistema que disipe
el calor generado y sea transmitido a la atmósfera, el sistema de refrigeración.
La refrigeración por líquido es muy efectiva y fue muy común en los primeros aviones,
los problemas surgieron cuando los aviones cada vez volaban más alto y se
producían grandes fugas de refrigerante debido a que el agua hierve a
menor temperatura cuanto menor es la presión.
El método que actualmente se utiliza es el método de refrigeración por circulación
forzada. Consiste en colocar tabiques o bafles y juntas de sellado que delimitan en el
interior de la carena en una zona de alta presión y otra zona de baja presión en donde
el aire es forzado a pasar entre los cilindros por gradiente de presión. La zona de alta
presión se encuentra situada en la mitad superior de la carena del motor aproximadamente
y recibe la corriente de impacto por la tomas de aire. La zona de baja presión esta
inmediatamente situada debajo de está en la mitad inferior de la carena y puede
tener una trampilla para regular el flujo de aire.
La refrigeración forzada permite obtener máxima refrigeración con mínima ingestión de
aire en el interior y por tanto menos resistencia aerodinámica.
Temperatura
de culata
La temperatura del motor se supervisa
mediante el indicador de temperatura de culata. Ya vimos que la culata de cilindros
era la zona más caliente, es donde vamos a tomar la temperatura por medio de un termopar.
La temperatura de culata se presenta en una escala de 0º a 350º normalmente. Con
lecturas normales la refrigeración resulta efectiva.
(Colaboración de Roberto Fernández para AirHispania).
|